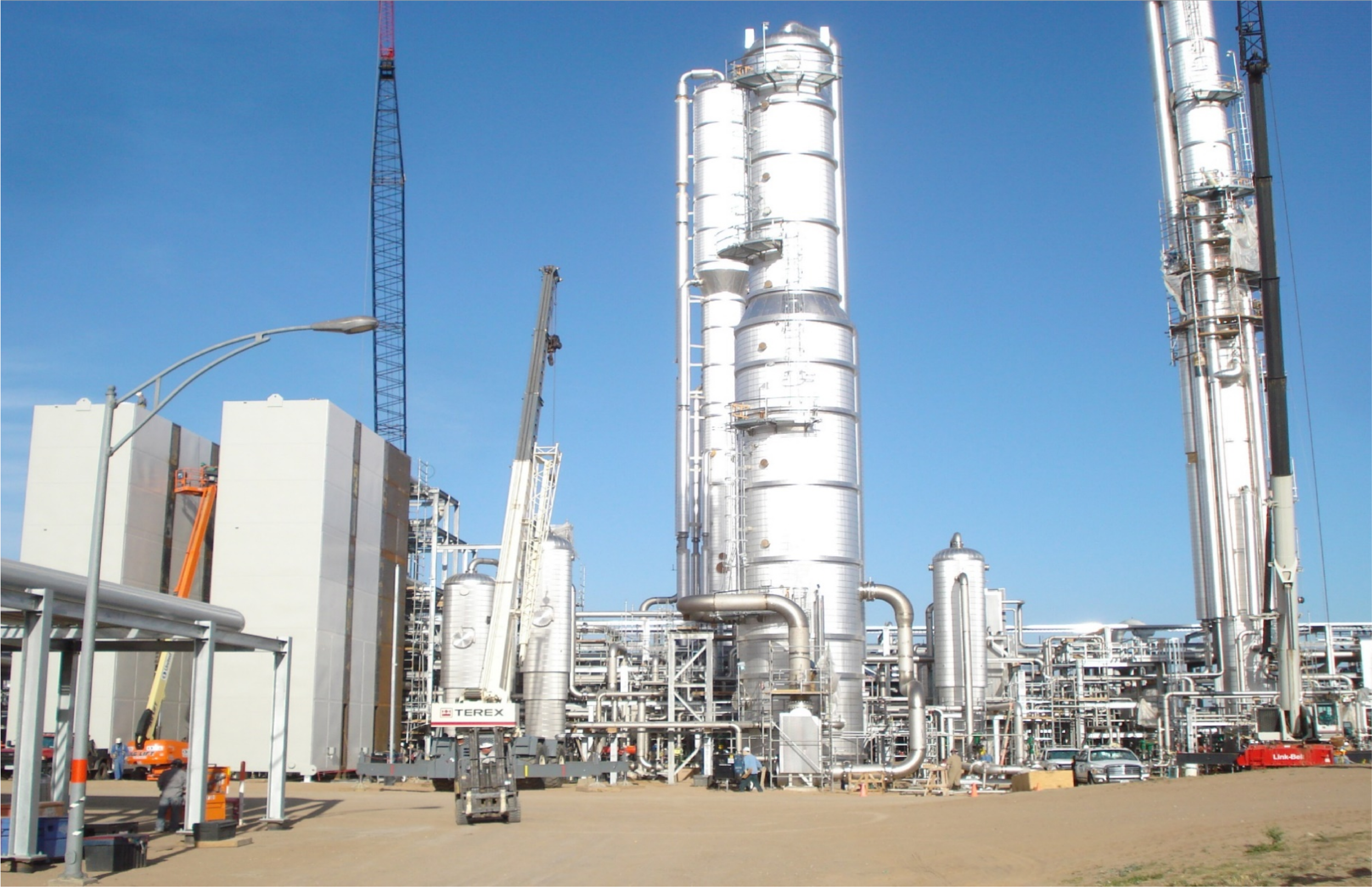
Azota Is Your Trusted Partner for Nitrogen Rejection Units (NRUs)
Azota is Headquartered in Houston, Texas serving Nationwide
Azota is a pioneer and industry leader for cryogenic nitrogen rejection units and helium recovery. With our line of nitrogen rejection units, with its first-of-its-kind dual tower design, Azota has been pushing the industry forward for decades.
The Need for Nitrogen Rejection in Natural Gas Processing
Natural gas, a crucial energy resource worldwide, often contains nitrogen, which can lower its energy value and complicate transportation and usage. With nitrogen levels as low as 3-4% causing issues in pipeline specifications, it becomes imperative to efficiently and effectively remove nitrogen from natural gas. This is where Azota Gas Processing steps in, offering state-of-the-art solutions in nitrogen rejection.
Unmatched Experience
Azota founders developed the first gas plant-style, non-cold box design NRU in the 1980s
Designed and built the first dual-column NRU with an integrated liquids recovery plant
Created the first dual-column NRU with integrated helium recoveries
System Capabilities
Both standard and customized designs are available in sizes from <5 to 100+ MMSCFD per day
Our NRUs can handle inlet pressures as low as 550 psig all the way up to 1000 psig
System can handle a wide range of nitrogen feed concentrations: <5-90%
Product streams can be processed down to less than 1% N2
Nitrogen vent streams with less than 1% hydrocarbon are possible
Helium recoveries of 95% or more (when applicable)
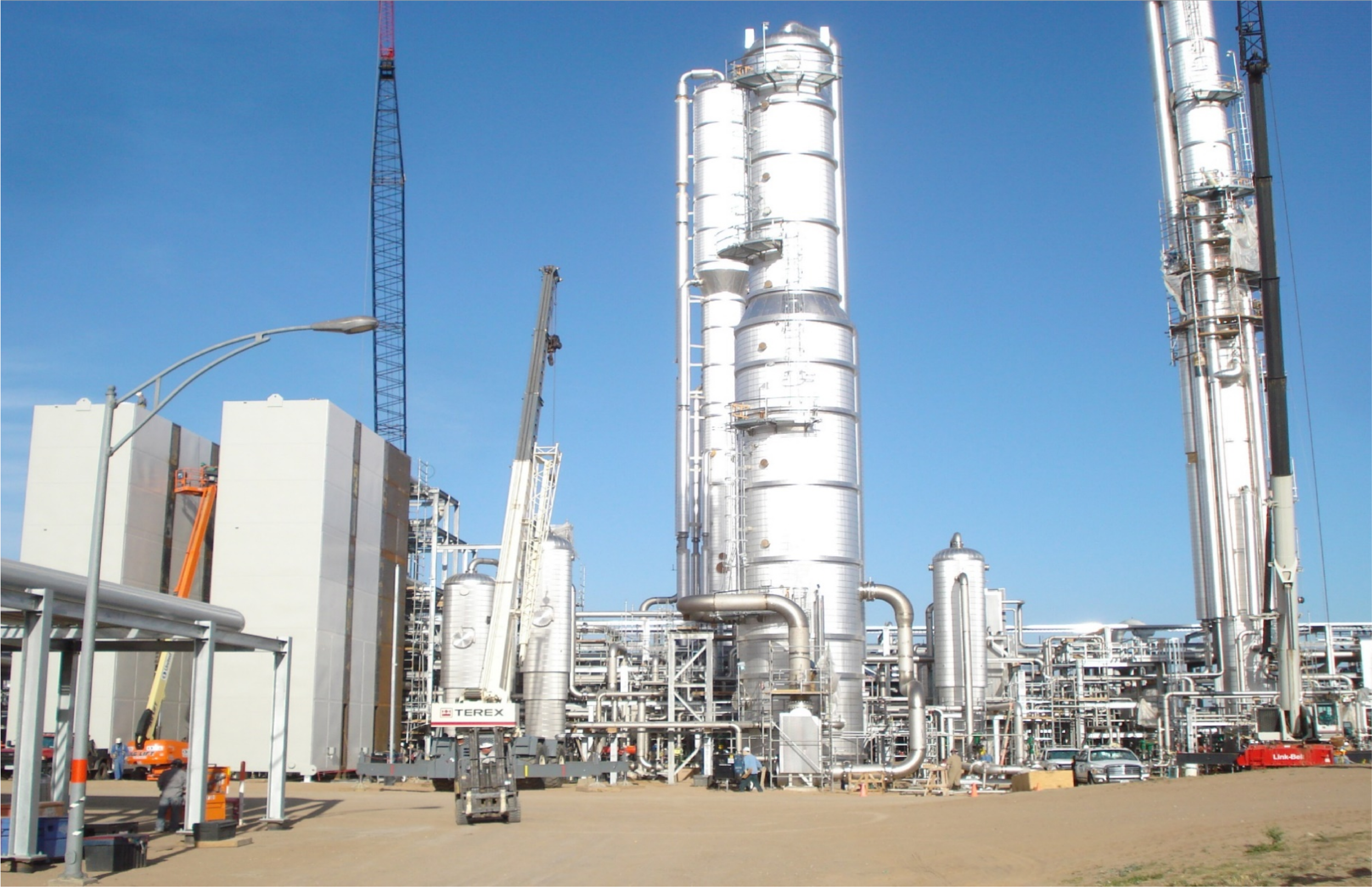
"Where Excellence Meets Efficiency"
At Azota, hearing "It’s our best running plant!" is not just an accolade, it's our standard. Our approach to building gas processing facilities is rooted in a blend of cutting-edge technology and operational excellence, ensuring every plant we build becomes a benchmark in the industry.
We Service The Following Areas for Nitrogen Rejection Units
Texas
Oklahoma
Kansas
Azota’s Years of Experience with Helium Recovery
The Azota team’s first helium recovery plant was designed and built in 1988 in conjunction with a nitrogen rejection unit and liquids recovery plant in Utah’s Lisbon Valley. This plant remains in operation to this day. We have continued to expand our helium recovery and nitrogen rejection capabilities on many projects since. Today, with depleting helium supplies, we focus on solutions increasing helium recovery and are finding situations previously thought not commercially viable to be worth further consideration.
Helium Recovery and Purification
There are some helium containing gas wells in every one of the contiguous North American states. Usually these occur where high nitrogen content gas is found. Azota believes that as the scarcity of this rare gas increases, more businesses will investigate the possibility of recovering the helium they are currently venting or sending down the sales pipeline.
Helium Supply & Demand
With the Federal Helium Reserve depleting its inventory and privatization taking hold, helium demand is expected to be well more than supply for years to come (as seen in the chart below). This scarcity is certain to drive further investment and need to capture this finite resource. Azota is well-equipped to evaluate and add helium recovery to your processing and treating facilities as it becomes more commercially attractive.
Azota’s Helium Recovery Processes
Cryogenic Recovery
Helium recovery plants are typically associated with nitrogen rejection units (NRU’s). These deep cryogenic plants permit the integration of the helium recovery equipment particularly if the need is foreseen before the NRU design and construction. Helium recoveries can be >98%.
Adsorption Recovery
A non-cryogenic process may also be used for the recovery of helium. Based upon the same pressure swing adsorption technology used for helium and hydrogen purification, these units are dependable, robust, and commercially viable for many smaller applications.
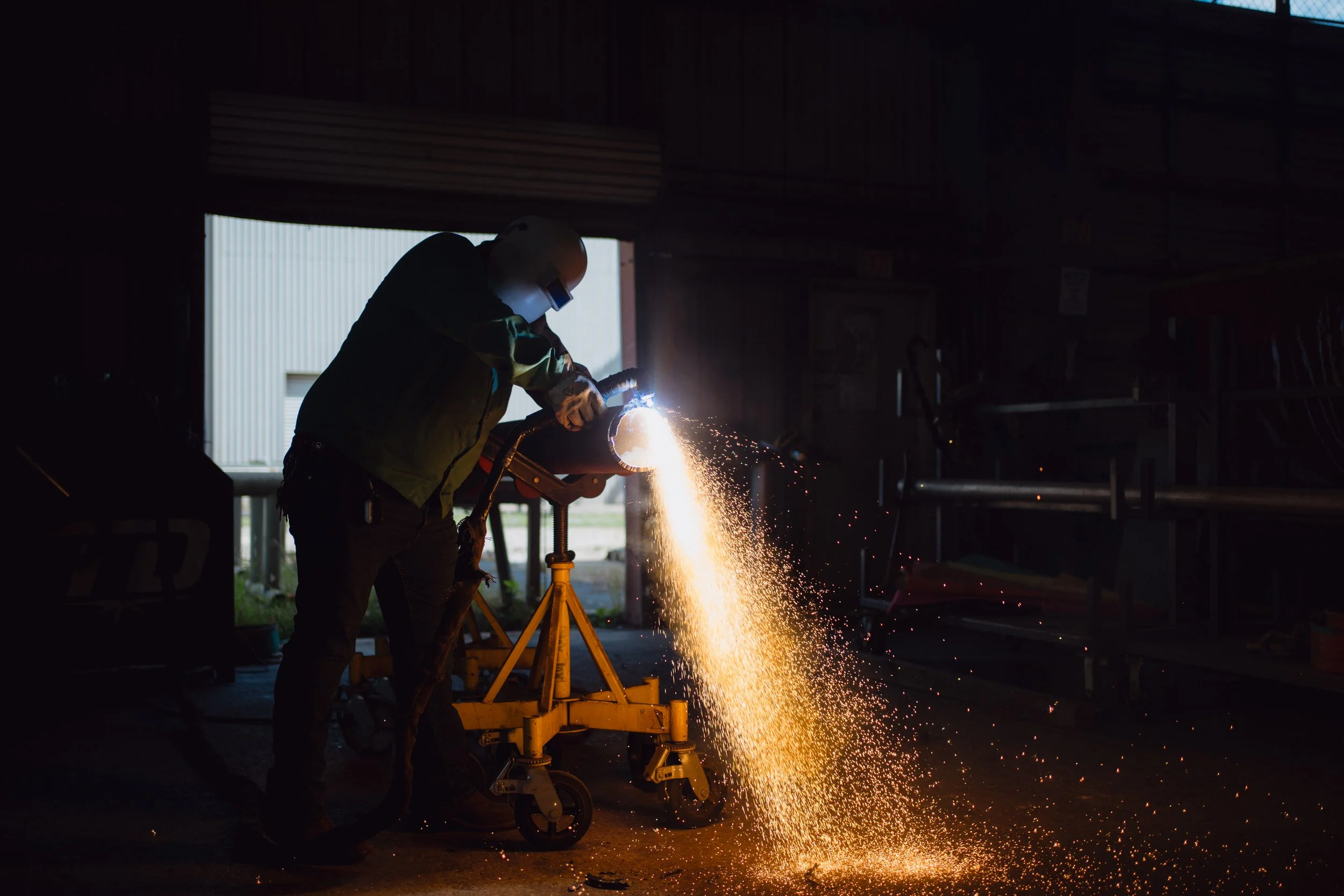
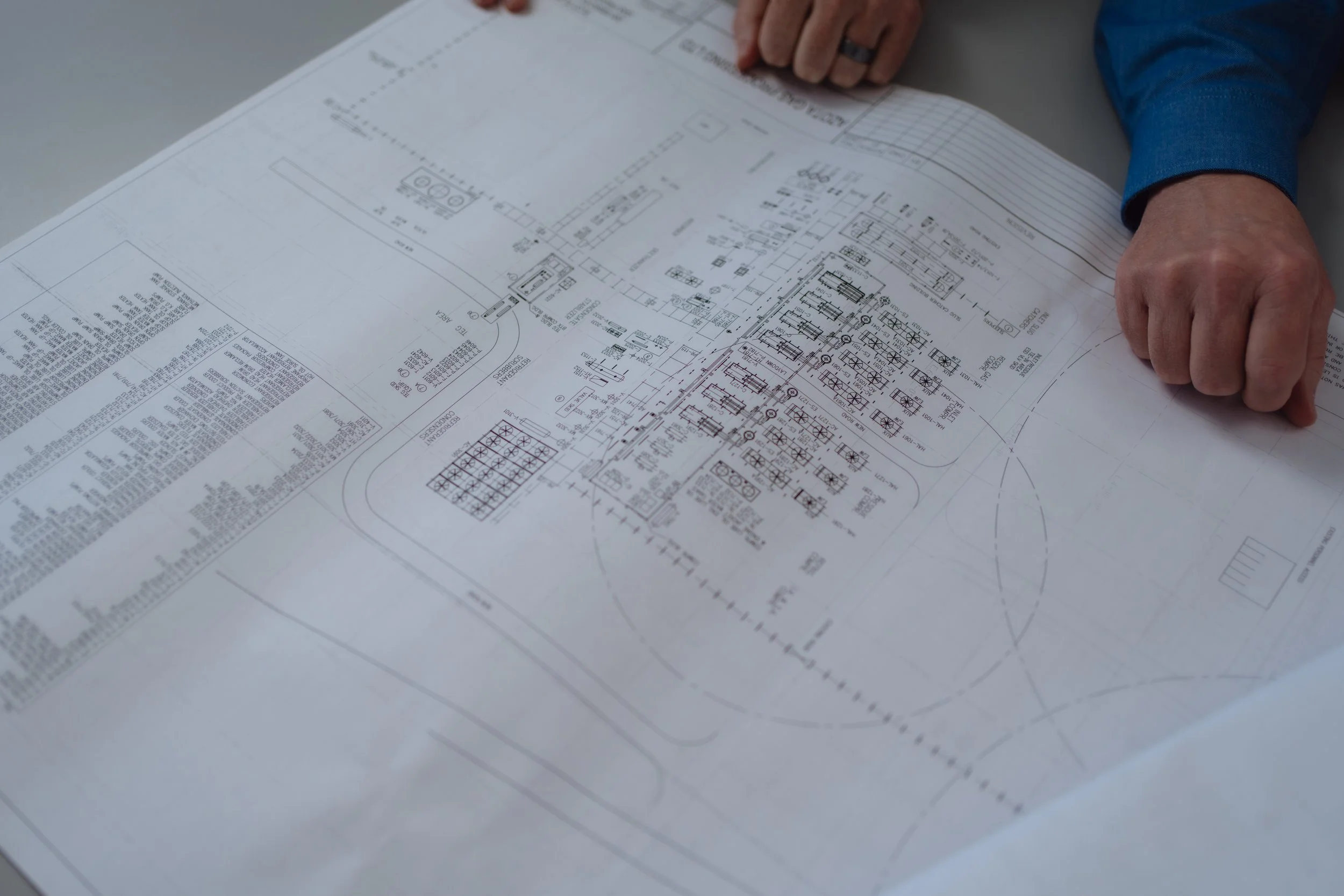
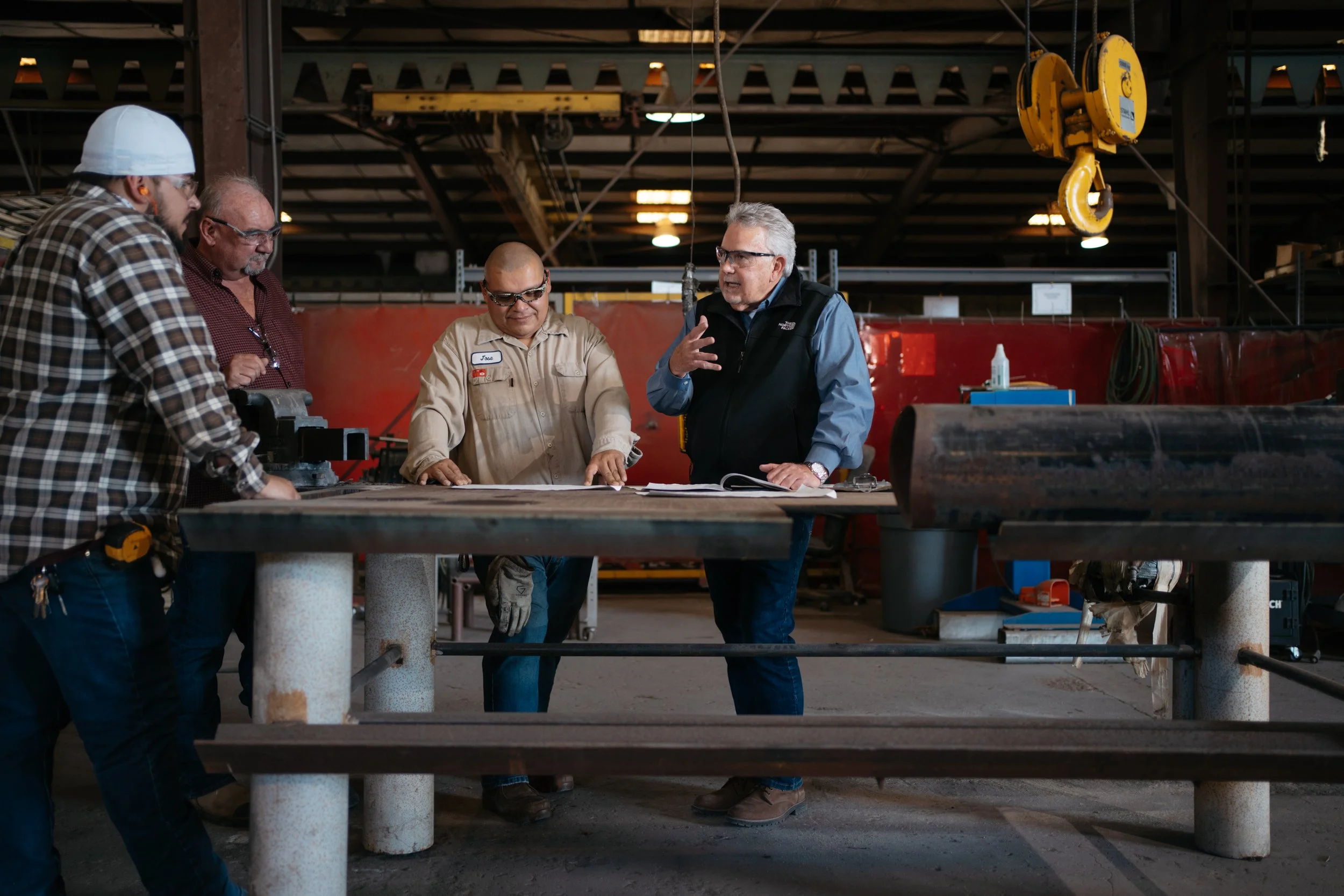
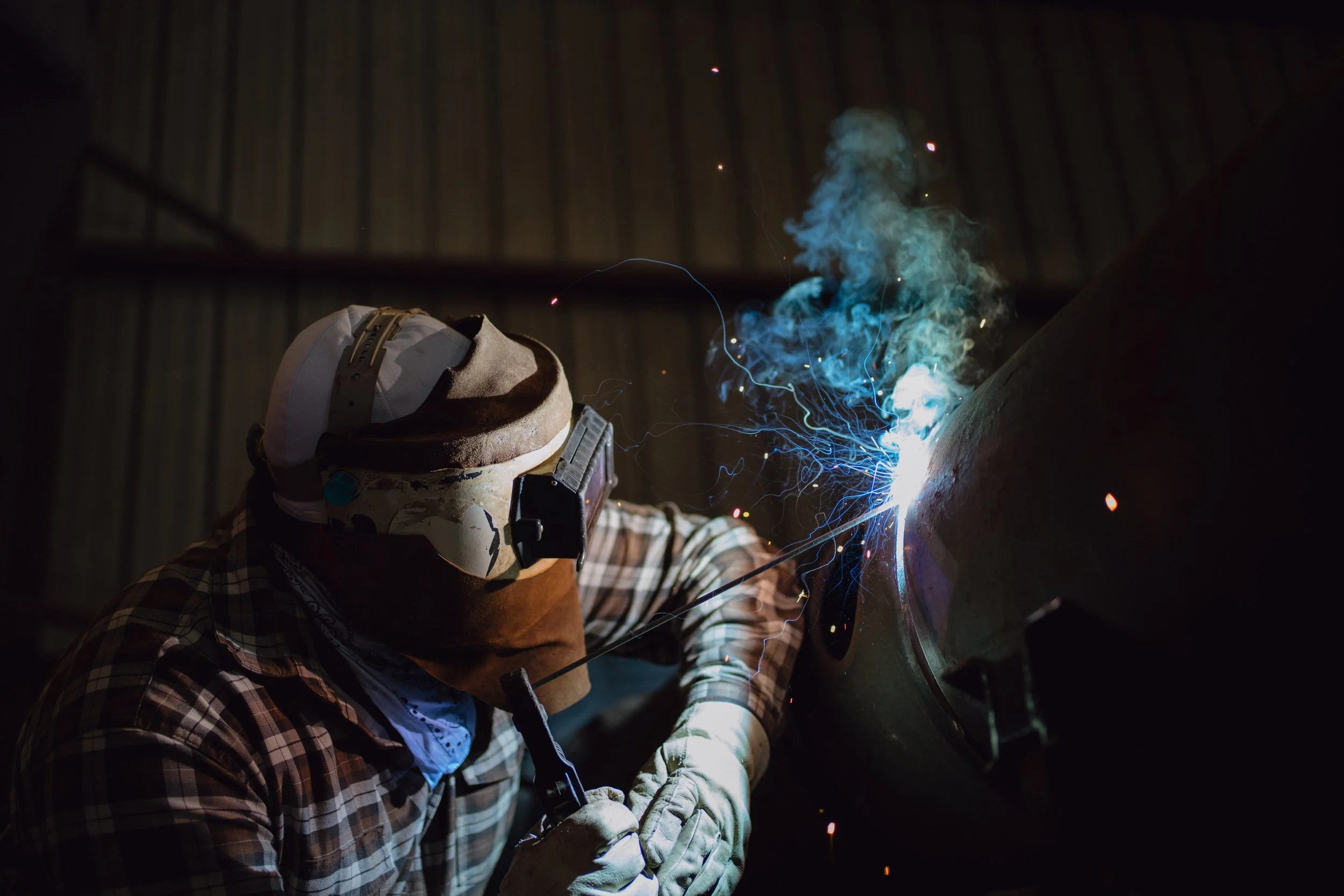
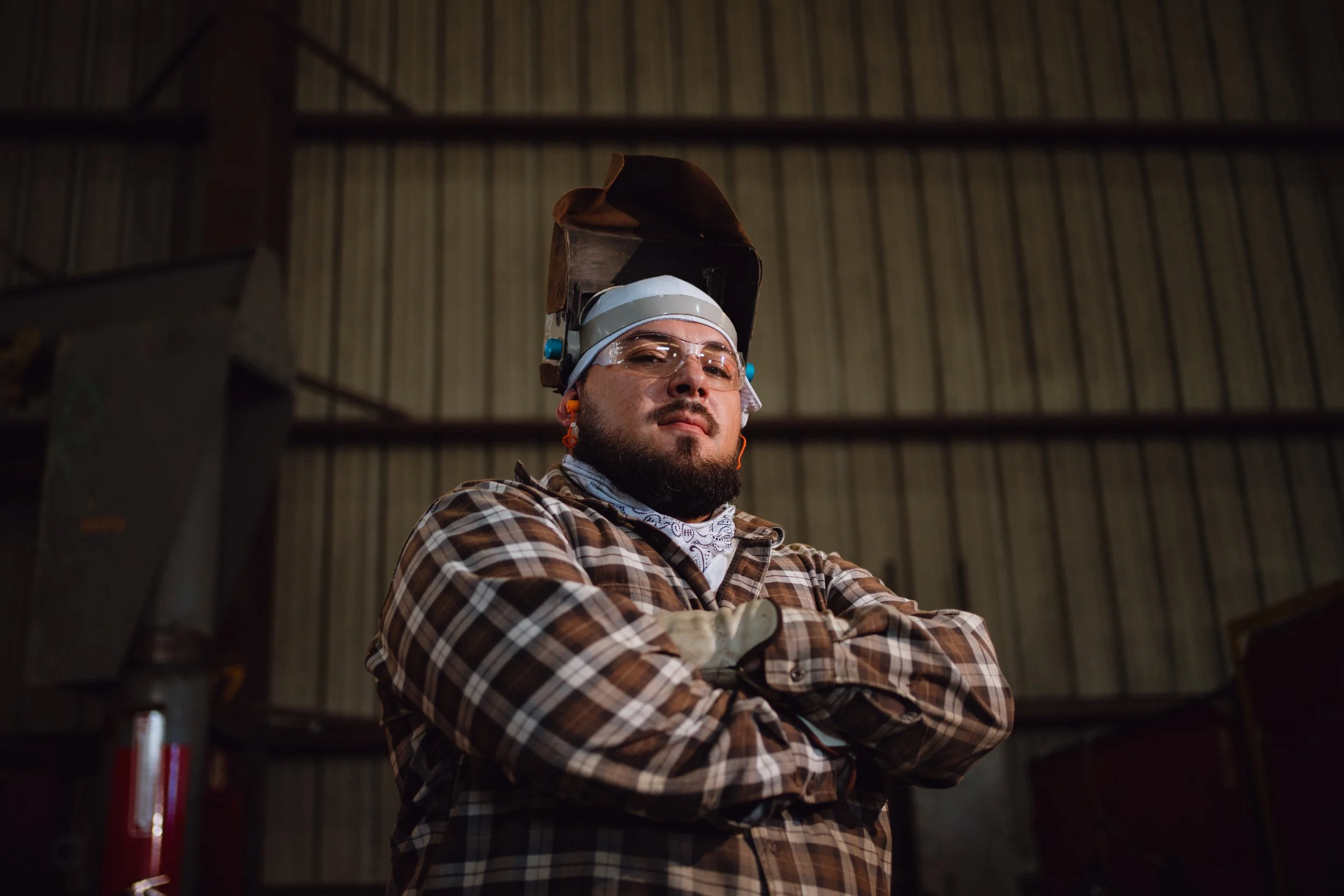
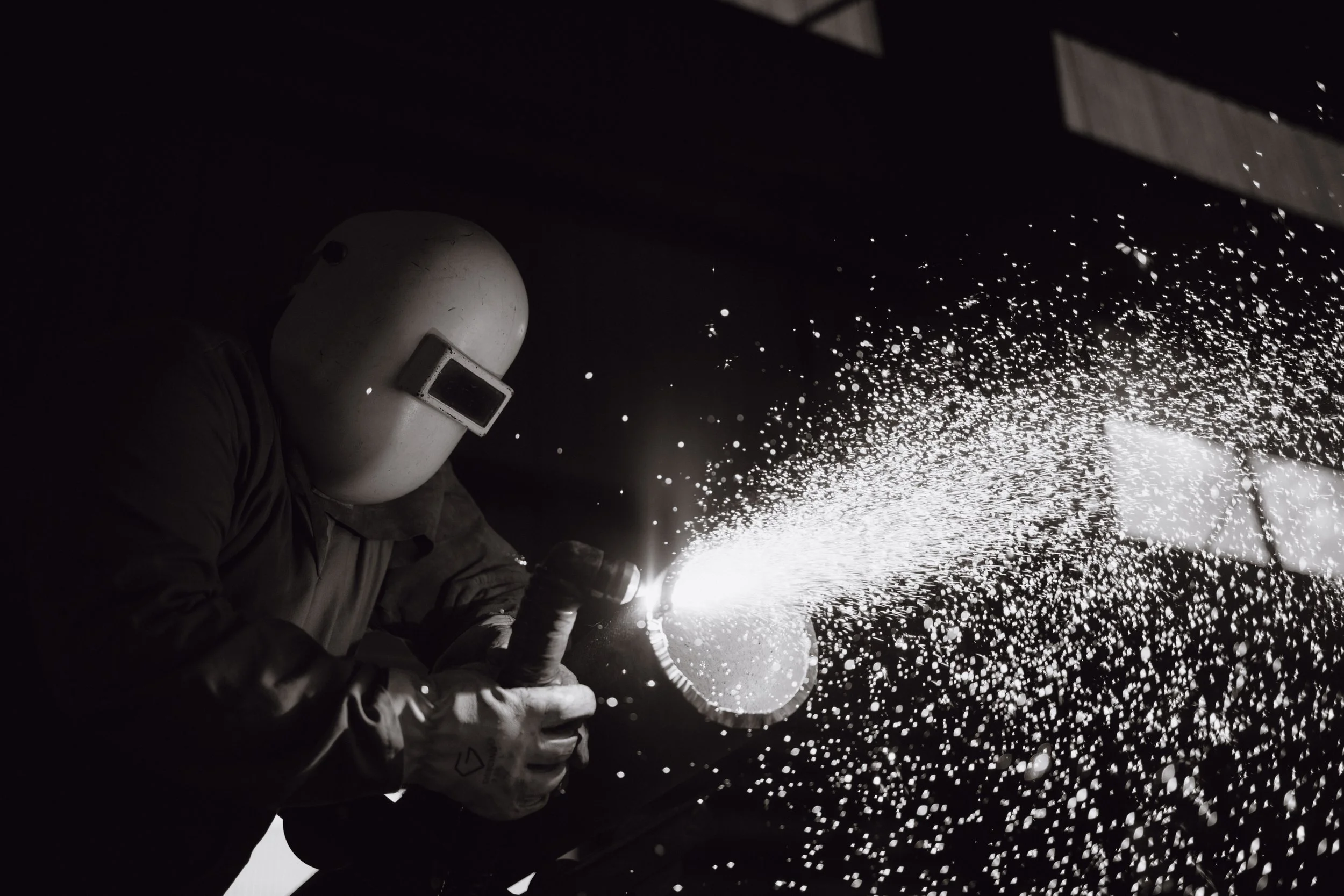
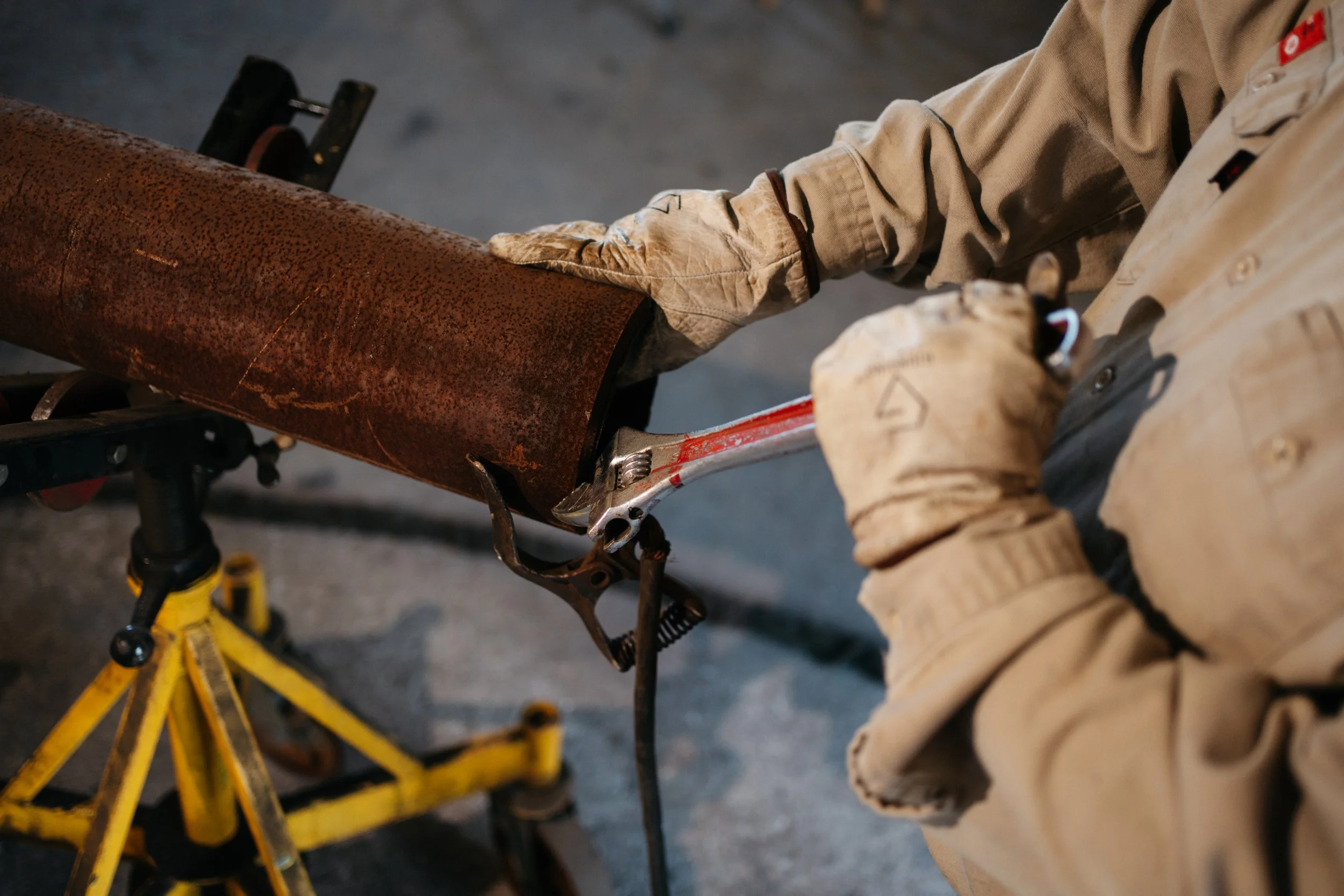
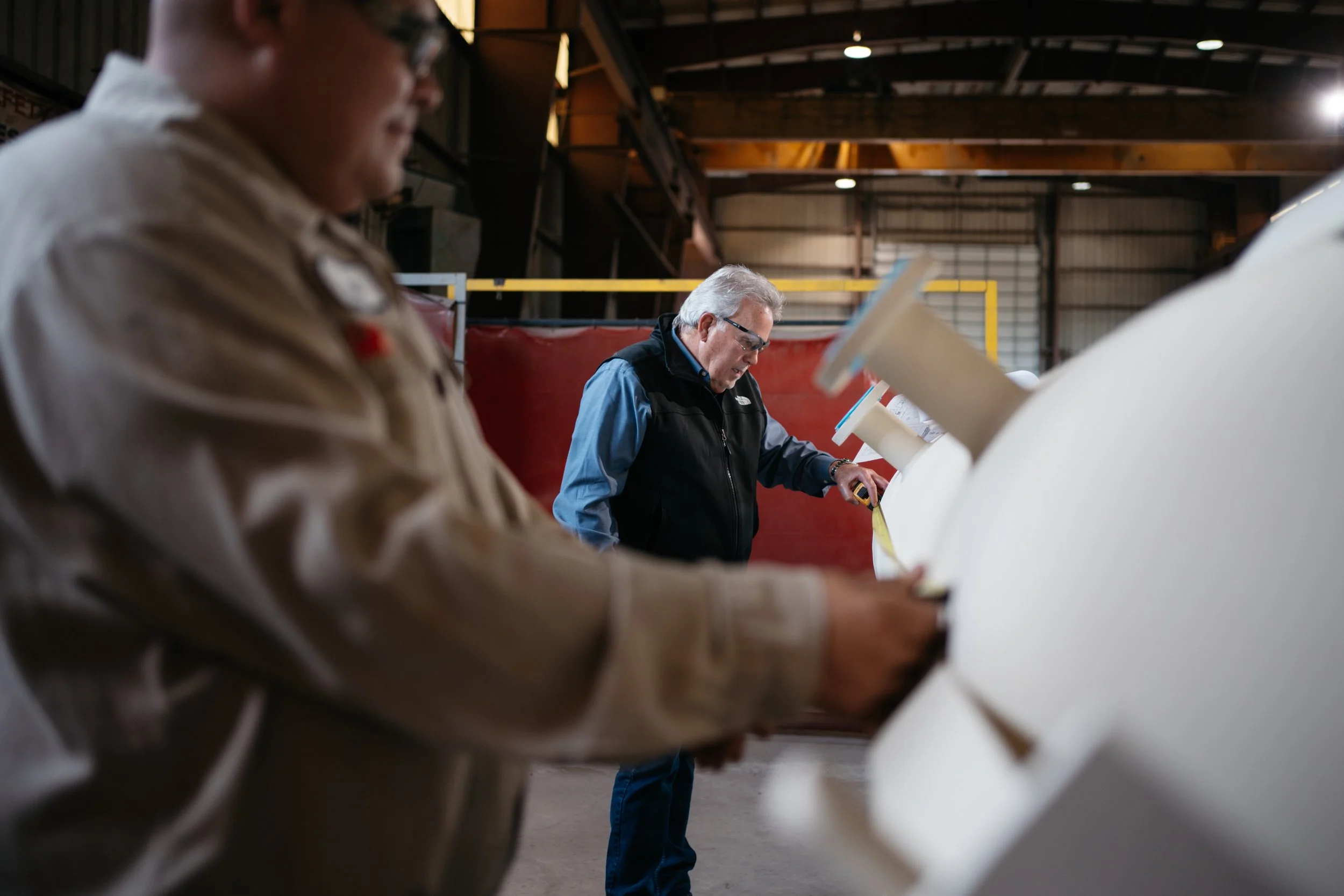

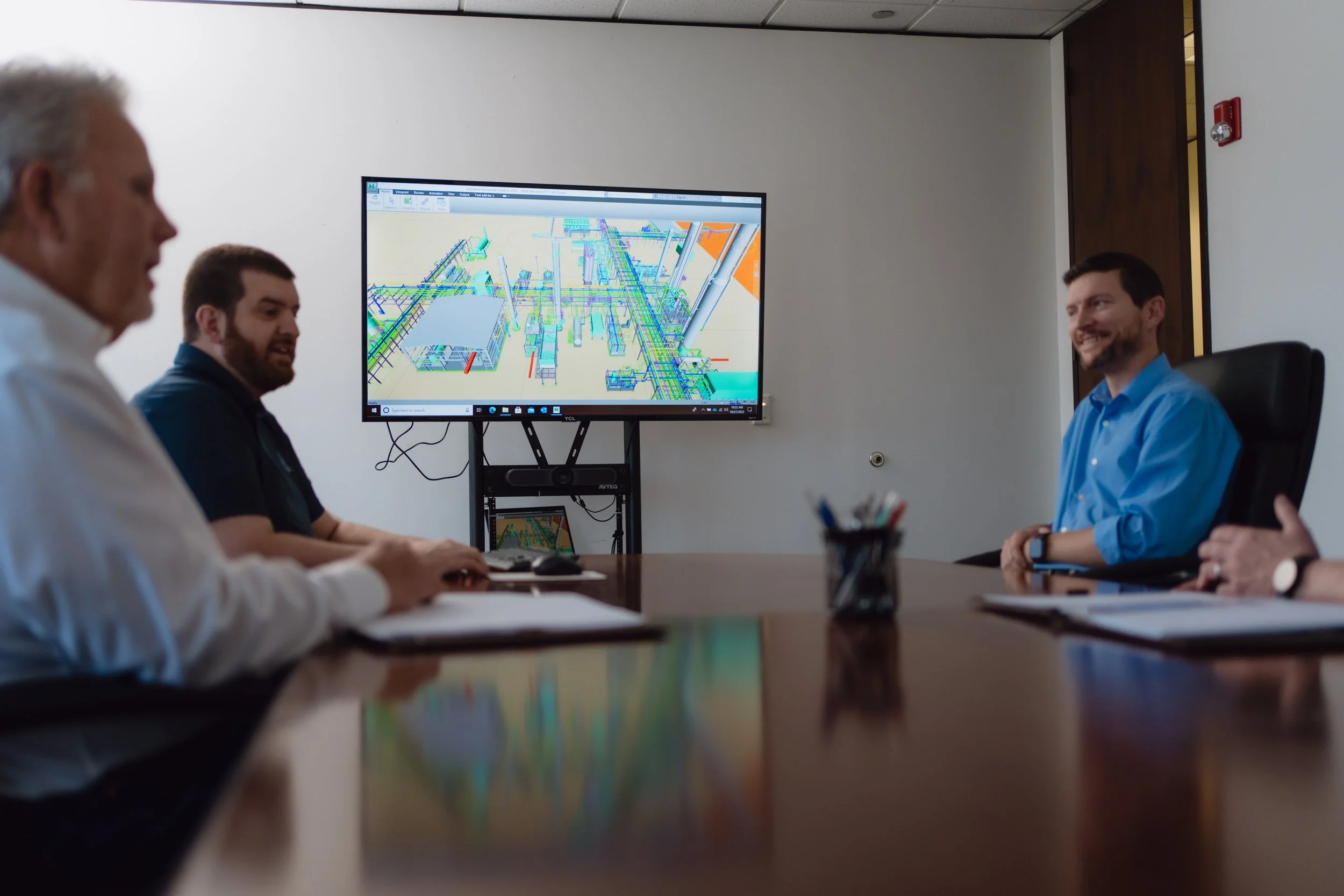

The Azota Difference
Our systems are able to outperform the competition because we have utilized our vast experience to focus on overdesign of our system in several key areas:
More Insulation
More Exchanger Surface Area
Additional Tower Trays
Azota also has the complete portfolio to provide the other processing systems to prepare feed for deep cryogenic processing:
-
Azota provides both standalone Acid Gas Removal Units (AGRU) and units part of a turnkey natural gas processing plant suite. These units ensure thorough removal of acidic components such as CO2, H2S, mercaptans and COS. We are the only designer of split flow, high efficiency amine systems capable of meeting <10 ppm CO2.
Learn more (add hyper link to amine treating for acid gas removal) (amine-treating)
-
Molecular Sieve is the tried and true solution to most deep cryogenic gas plant dehydration applications. These systems are robust and easily operated either remotely or in manned gas plant applications. We have designed one, two, three and four bed systems. As with all gas processing applications Azota has engineered some attractive energy saving variants on the typical molecular sieve system.
Learn more (hyperlink to gas dehydration) (/gas-dehydration)
-
Ethane Recovery - As the industry has required higher ethane recovery levels, Azota has refined our basic turbo expander plant design, while maintaining horsepower efficiency, so that our customers may expect ethane recovery levels in excess of 99%. These facilities are practical and provided on a license-free basis.
Propane Recovery - The shale gas boom revealed a need for an uncompromised design for a high-propane recovery plant capable of full ethane rejection. Azota’s propane recovery plant design allows low inlet gas pressure in a turbo-expander is not necessary, as well as lower residue gas recompression requirements.
Learn more (link to /cryogenic-ngl-recovery-plants/)
Azota’s Top NRU Projects
620 MMSCFD Nitrogen Rejection and Helium Recovery Plant | Liberal, KS
Turnkey design, engineering and construction of a 620 MMSCFD Nitrogen Rejection and Helium Recovery Plant with 93+% ethane recovery, 97% Helium Recovery, and 99.9% total hydrocarbon recovery using proprietary double column NRU technology. The plant was integrated into an existing Helium Recovery Facility that did not previously provide for nitrogen rejection. The Project included installation of 44,000 BHP of motor-driven centrifugal gas compression, a 650 GPM Inlet Gas Treater utilizing MDEA, a 110 GPM TEG Dehydration, and two Regenerative Thermal Oxidizers – one for the amine vent and one for the nitrogen vent.
add-on 35 MMSCFD nitrogen rejection unit | Midland County, Texas
Engineering study for an add-on 35 MMSCFD nitrogen rejection unit. The NRU treats residue gas from the existing cryogenic plant to less than 2% N2 while recovering 99.9% total hydrocarbons.
75 MMSCFD NGL recovery, nitrogen rejection, and helium recovery plant | Cimarron County, Oklahoma
Engineering and design study of 75 MMSCFD NGL recovery, nitrogen rejection, and helium recovery plant. Plant capable of 95+% ethane recovery, 97+% helium recovery, and 99.9% hydrocarbon recovery using an integrated NRU design with proprietary double column technology. Project also includes 1000 BPD slug catcher and condensate stabilization, 50 GPM amine treating and regeneration, mole sieve dehydration, propane refrigeration, and inlet/residue compression.
35 MMSCFD Plant | Eustace, TX
Turnkey engineering, design, procurement, and construction associated with the redesign and upgrade of a non-functioning Nitrogen Rejection Plant. The Plant was redesigned to process 35 MMSCFD of high nitrogen inlet gas while recovering 90% of the contained ethane in a liquid product steam and producing a residue gas stream with 99+% hydrocarbon recovery.
50 MMSCFD high ethane recovery plant with integrated NRU and helium recovery | Potter County, Texas
Engineering study for the redesign and optimization of the existing plant cryogenic liquids recovery, nitrogen rejection, and helium recovery systems. Study included design for a 50 MMSCFD high ethane recovery plant with integrated NRU and helium recovery. Plant was capable of 93+% ethane recovery, 95% helium recovery, and 99+% hydrocarbon recovery. Plant design to utilize existing gas treating, compression, and mechanical refrigeration systems.
10 MMSCFD NRU Plant | Petrolia, TX
Azota owned and operated 10 MMSCFD NRU. Plant included amine treatment, glycol and mol sieve dehydration, with turbo-expander type NGL recovery process. NRU employed single tower design with 99% total hydrocarbon recovery.
Services We Offer With Every Solution NRUs
Check Out Our Other Services